Почти тысяча двести человек сегодня работают на крупном по белорусским меркам предприятии — Гомельском вагоностроительном заводе. Здесь строят и ремонтируют вагоны более чем пятидесяти видов и по многим экономическим критериям опережают показатели работы промышленности в целом по стране. При этом завод не просит помощи у государства, всегда рассчитывает только на свои силы. Накануне Дня железнодорожника журналисты «Белки» побывали в цехах и на производственных участках, поговорили с людьми и узнали 10 интересных фактов о заводе.
1. В ремонте вагонов используется до 90% деталей из кузнечно-механического цеха
Прежде чем закрепиться на вагоностроительном заводе, Владимир Самуйлов успел поработать на «Коралле» и «Гомсельмаше». И везде был слесарем механосборочных работ. В 90-е многие производства останавливались, а железнодорожники продолжали ремонтировать свои вагоны. По совету друзей Владимир Сергеевич пришёл на свободное место.
— Кузнечно-механический цех при мне уже неоднократно перестраивался и перевооружался. Под расширение убрали стеллажи и поставили на их место сварочные кабины. Станки заменили процентов на 70. Вот этот, горизонтально-сверлильный, за которым я сегодня работаю, самый свежий. Он в разы облегчил труд, — проводит бригадир экскурсию по вверенной ему территории.
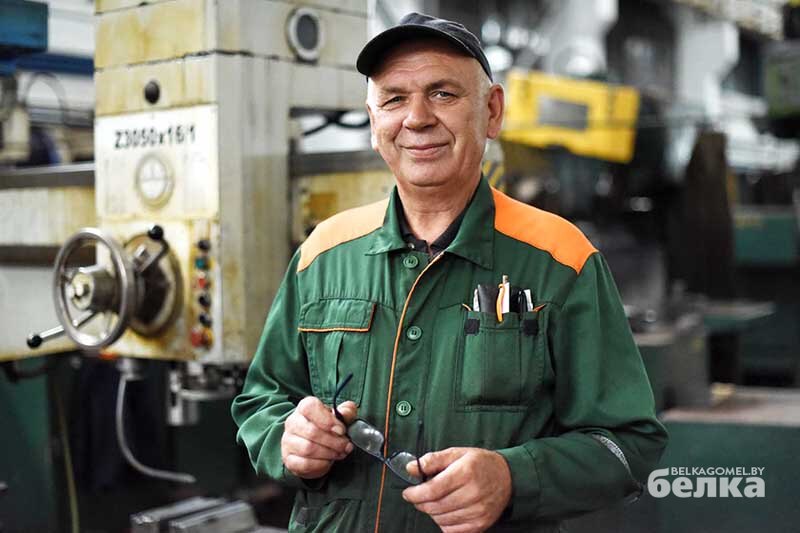
Владимир Самуйлов
В ремонте вагонов используется до 90% деталей, выходящих из ворот кузнечно-механического цеха. А это более двухсот наименований. Владимир Самуйлов мог бы перечислить их все, но на это ушла бы половина рабочего дня. Многие детали непосредственно влияют на безопасность перевозок, потому и контроль строгий.
— Каждая деталь по- своему сложная. Тот же подвижный упор для верхней полки. Пассажир на него и внимания не обращает. Но это только потому, что он с этой полки не падал. И не упадёт, пока мы отвечаем за качество своей работы. Вы не поверите, но на изготовление одной такой детали уходит до пяти дней, — акцентирует внимание Владимир Сергеевич.
Тем не менее работники цеха успевают работать как на нужды своего завода, так и для сторонних предприятий. На днях передали заказчику 180 личинок для замков тамбурных дверей из отполированной нержавеющей стали.
2. На электроначинку одного вагона нужно от 40 до 90 аккумуляторов
С выбором постоянного места работы Василий Осипенко определялся недолго. После армии год побыл электриком на «Гомсельмаше» и перешёл к железнодорожникам слесарем. Семь лет назад здесь же, на производстве, освоил новую для себя профессию — аккумуляторщик.
Это было вызвано технологической необходимостью. В одной из бригад после ухода человека на пенсию долгое время не было нужного специалиста, и руководство предложило закрыть вакансию своим же проверенным человеком. Чуть позже обновился весь состав бригады, а Василий Григорьевич её возглавил.
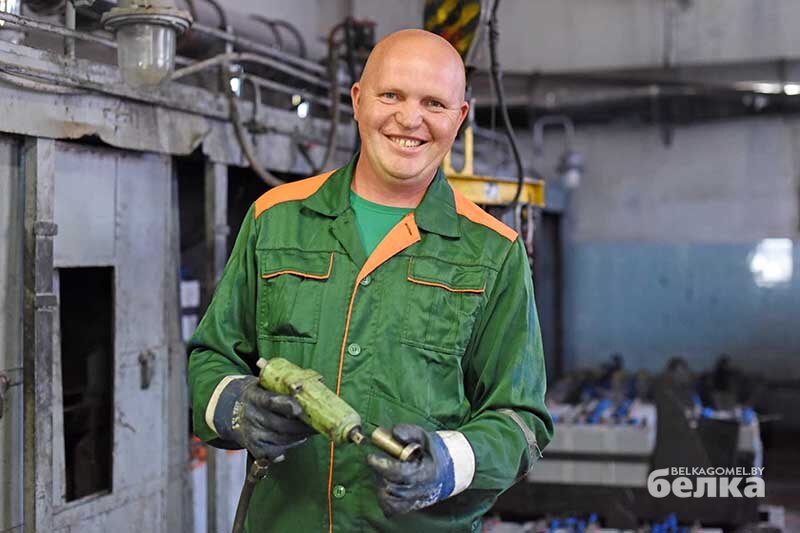
Василий Осипенко
— На самом деле в этой работе нет ничего сложного. С вагона снимается аккумулятор, ремонтируется, моется и заряжается. Принцип его работы ничем не отличается от автомобиль ного. Только в вашей машине аккумулятор один, а в вагоне их от 40 до 90 штук. В тех вагонах, что постарше, аккумуляторов меньше: там кроме света и кипятильника ничего не было. А в более свежих электроустройств больше. Тут и розетки на 220 В к каждому пассажирскому месту, и кондиционер, и холодильник с микроволновкой, и много чего другого. Вот и ёмкость нужна соответствующая, — проводит параллели Василий Осипенко.
В бригаде под его началом работают пять человек. Как говорит бригадир, коллектив маленький, потому и дружный. Каждый знает характер друг друга, его увлечения и проблемы, поэтому находить общий язык с подчинёнными легко.
3. Интерьерные решения определяют заказчики
Александр Соколюк более тридцати лет работает обойщиком в деревообрабатывающем цехе. На завод пришёл сразу после службы в армии в 1988 году.
— Дали мне наставника — и вперёд: учись делать поездки советских граждан более комфортными, — вспоминает начало начал Александр Антонович. — В мою задачу с первых дней входило обивать новые сиденья в «элитных» вагонах — купейных и вагонах-ресторанах. Главные рабочие материалы — поролон и дерматин.
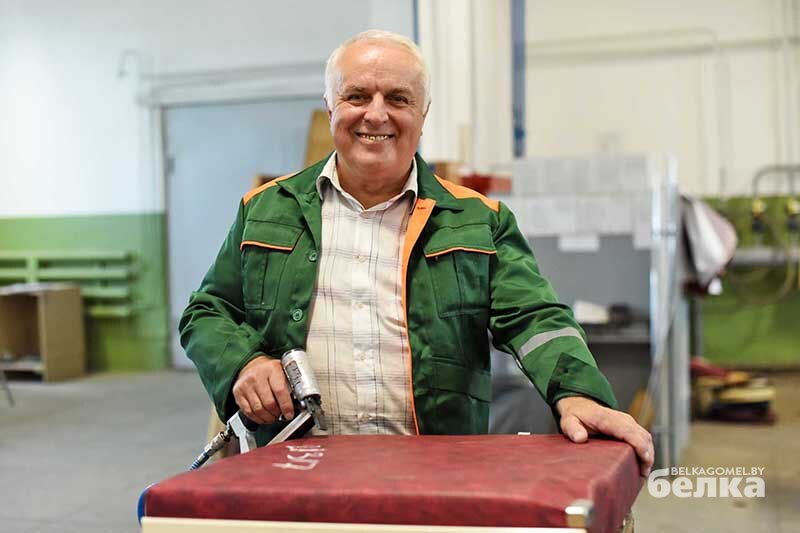
Александр Соколюк
По словам опытного обойщика, интерьерные решения определяют заказчики. Например, казахстанцев одинаково устраивают дерматиновые полки красного и синего цветов. Когда ремонтировали вагоны для украинцев, использовали только велюр.
— Тем, кто скажет, что у меня скучная и монотонная работа — день за днём вертеть туда-сюда одни и те же полки и жать на кнопку пневмопистолета, отвечу так: «Не в моём характере бегать с места на место и искать где лучше. Я на заводе уже 32 года. Руководство эту преданность ценит. У меня хорошая зарплата, приличный соцпакет, в коллективе пользуюсь уважением».
4. Заводская котельная пережила глубокую модернизацию
Первый раз на завод Вячеслав Тимошенко попал в 1979 году ещё во время практики от строительного училища. Успел немного поработать до службы в армии, ремонтировал вагонную мебель. Через пять лет снова вернулся на завод.
— Мать, отец и жена работали в энергосиловом цехе, и в 1990-м я тоже написал заявление, чтобы быть ближе к семье. Назначили оператором котельной, — вспоминает Вячеслав Валерьевич. — На моих глазах котельная пережила глубокую модернизацию. Когда пришёл, демонтировали угольные котлы и перевели цех на экологически чистый природный газ. Котёл выдаёт до 10 тонн пара в час. Этого достаточно для отопления и горячего водоснабжения всего завода и прилегающего жилого микрорайона.
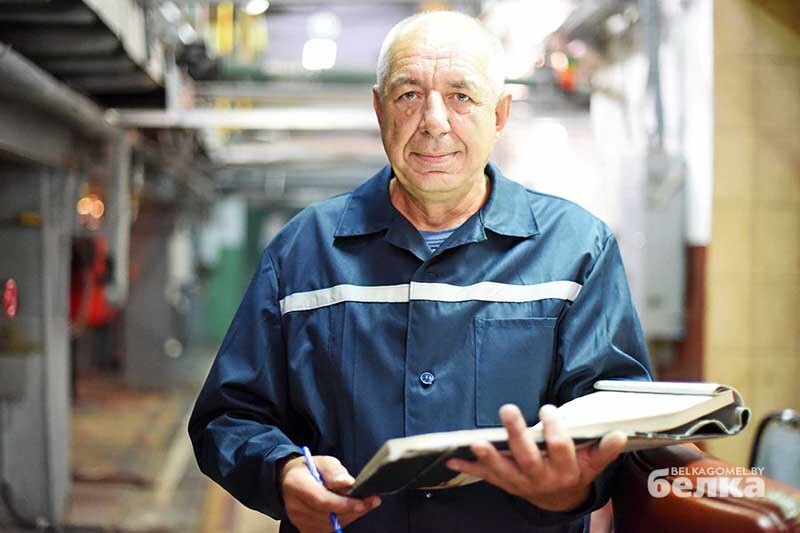
Вячеслав Тимошенко
В последнее время были установлены новейшие системы управления и безопасности. С прошлого года вся работа котла управляется компьютером. Нововведение шоком для персонала не стало.
— Если понимаешь процессы, происходящие внутри котла и во всех его клапанах, то переучиваться очень легко, — отмечает Вячеслав Тимошенко. — Но несмотря на всю автоматику, без человека в цехе не обойтись. Такое оборудование нельзя оставлять без присмотра ни на одну минуту. Техника техникой, а в случае сбоя оператор должен принять решение не за минуты, а секунды. Ведь пар под огромным давлением может натворить дел.
5. Местные заказы — это чаще всего деповской ремонт
К нынешнему празднику сгонщик-смывщик краски и лаков Анатолий Герасименко наработал 35-летний стаж в одном и том же цехе — разборочно-комплектовочном. Пришёл на завод сразу после армии.
— Первым инструментом, который мне вручили, был отбойный молоток. На то, чтобы снять краску с одного вагона, уходило до недели. Труд не для слабаков. Лет пятнадцать назад завод закупил углошлифовальные машинки, и процесс пошёл в разы быстрее, — рассказывает Анатолий Витальевич.
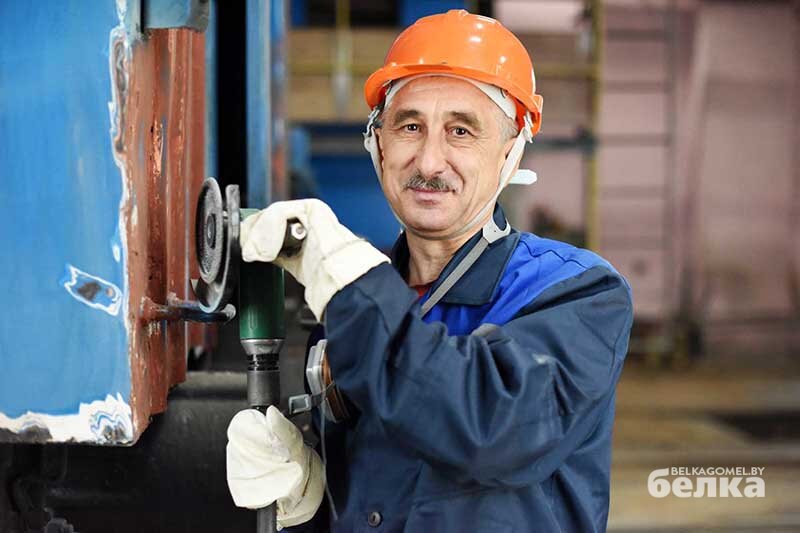
Анатолий Герасименко
В цехе есть установки для полного удаления слоя краски до металла. Они используются при выполнении казахстанского заказа. Из этого государства вагоны в Гомель поступают на капитально-восстановительный ремонт, что означает их полную перестройку. Местные заказы — это чаще всего деповской ремонт, по сути — косметический. Реже выполняется капитальный ремонт первого объёма.
— Так что к каждой единице свой подход. Где-то достаточно грубой обработки поверхности, а где-то приходится и пылинки сдувать. В прямом смысле слова, — улыбается старожил.
За время работы Анатолий Герасименко успел не только внести собственный вклад в развитие завода, но и прикоснулся к его истории:
— Разборочно-комплектовочный цех находится в одном из старейших сохранившихся на заводе корпусов. Под вагоном, у которого мы сейчас стоим, раньше были канавы для ремонта паровозов. Их засыпали совсем недавно. Правда, я застал на этих путях уже только цельнометаллические вагоны.
6. В одну смену на заводе отливают две тысячи тормозных колодок
Свой трудовой путь Евгений Атрощенко начал в вагоносборочном цехе после окончания железнодорожного техникума. В «литейку» решил перейти по нескольким причинам: во-первых, более удобный график, во- вторых, выше заработок. Чтобы переучиться на шихтовщика, поехал на специальные курсы в Минск.
— Моя работа заключается в том, чтобы поставлять металл в чугунно-литейный цех на завалочную площадку. Я хоть и учился, но в практике был не очень силён. Старшие работники провели по цеху, спокойно и доходчиво объяснили весь процесс, и я понял, что втянусь, — вспоминает свой первый день на новом рабочем месте Евгений.
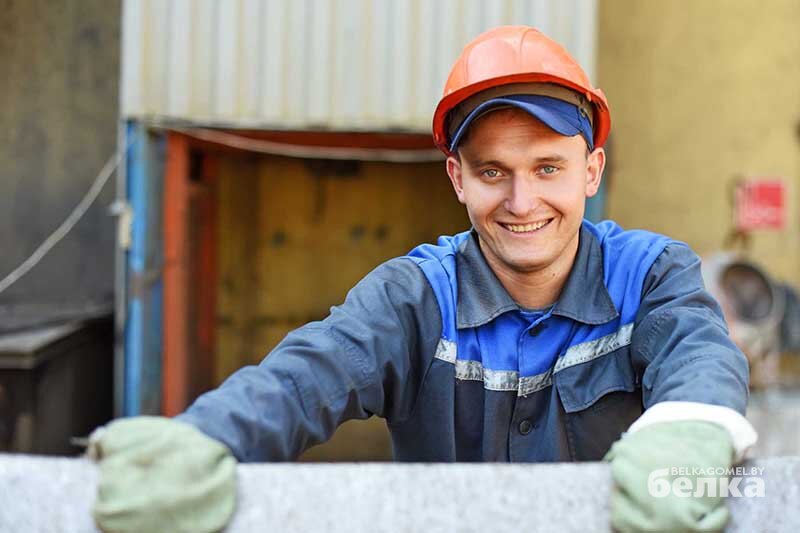
Евгений Атрощенко
Лом чугуна магнитной плитой загружается в вагонетку, которая подаётся непосредственно в цех. Здесь металл переплавляют и дают ему вторую жизнь. На этом участке Евгений и работает. Можно сказать, стоит в начале процесса, в результате которого получаются чугунные тормозные колодки для железнодорожного транспорта. Они расходятся по многим странам СНГ.
— Процесс непрерывный. Мы в одну смену отливаем две тысячи тормозных колодок. Одна весит 14 кг. Соответственно, нужно подать и загрузить в печь 28 тонн металла. Приходится только радоваться тому, что это делается не вручную, — смеётся Евгений.
7. Поступившие на ремонт вагоны нужно выгрузить строго по времени, иначе – штраф
Электромонтёр транспортного цеха Евгений Подлипский дату прихода на завод называет сходу. Это было 22 сентября 2003 года. Пришёл после Гомельского училища №152 приборостроения, которое окончил с красным дипломом. Уже тогда знал, чем хочет заниматься в жизни, поэтому и к учёбе относился очень ответственно.
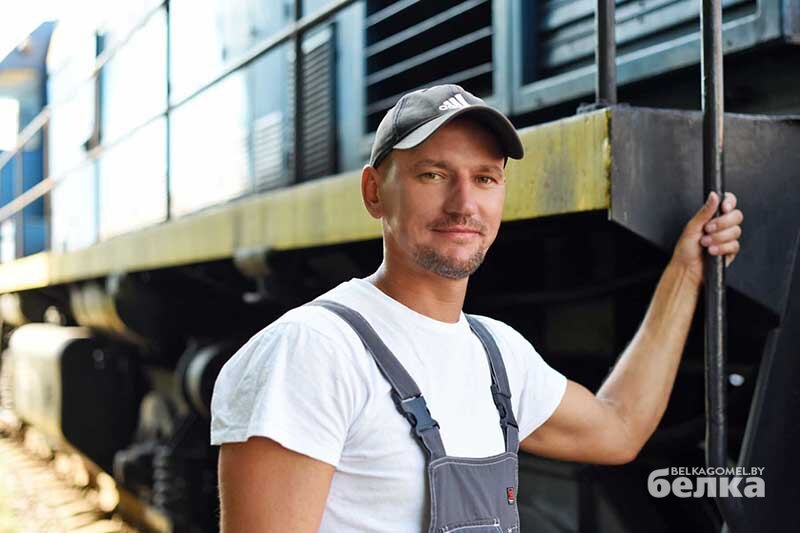
Евгений Подлипский
Транспортный цех обслуживает маневровые тепловозы и электрические железнодорожные краны.
— Вагоны, которые приходят на завод под выгрузку, имеют лимит времени пребывания на территории. Если за эти часы снять груз не получится, заводу выставят счёт за простой, а это большая сумма. Поэтому тепловозы и краны должны работать как часы, и мне эту работу доверяют, — рассказывает Евгений Подлипский.
На вопрос о том, кто научил его всему, что он теперь умеет, специалист без ложной скромности отвечает так:
— Самый лучший учитель — это сам я. Пока руками не потрогаешь, ничему не научишься. Образование при этом не имеет никакого значения.
8. Машинисты мостовых кранов должны быть универсалами
Знакомство с заводом у Ирины Колесниковой состоялось в 2012 году с колёсно-тележечного цеха, где она сегодня работает машинистом мостового крана. Правда, сесть за рычаги на высоте ей доверили только спустя два года.
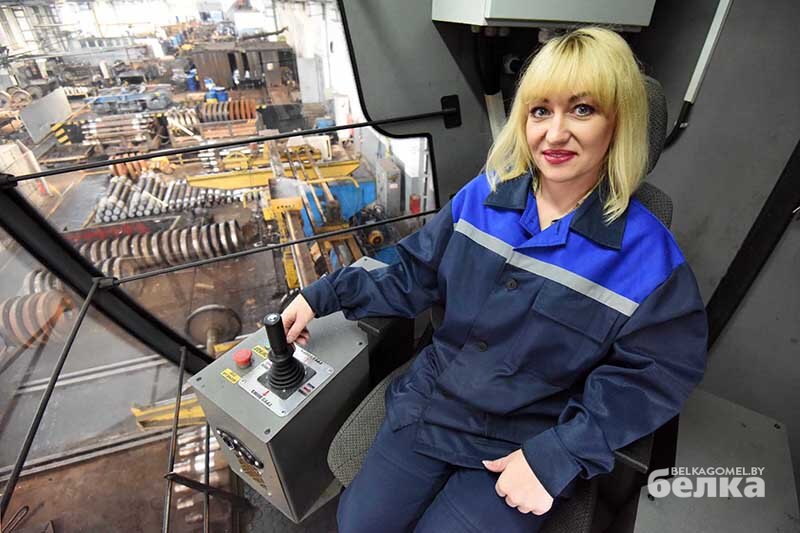
Ирина Колесникова
— Конечно, это произошло не просто так по моему желанию. Сначала я прошла полный курс в сертифицированном учебном центре, сдала квалификационный экзамен, а уж потом получила разрешение подойти к технике поближе, — вспоминает Ирина Анатольевна.
Времени на медитацию у машинистов кранов, а их в этом цехе шесть, не то что не хватает — его вообще нет. Всю рабочую смену приходится перемещать с участка на участок грузы. Это и колёсные пары, и тележки в сборе, и технологическая оснастка с другими приспособлениями.
— День на день не приходится — мы постоянно пересаживаемся с крана на кран. Сегодня я везу тележки, а завтра подаю колёса на запрессовку оси и так далее. Это неспроста. Если кто-то из коллег уйдёт в отпуск или заболеет, другой без проблем его заменит, так как уже знаком с каждым из участков. Впрочем, мы стараемся не болеть. Находиться на работе интереснее, чем на листке нетрудоспособности, — говорит машинист.
Вместе с Ириной на предприятии трудится её муж. Недавно семья Колесниковых одержала победу в заводском конкурсе на лучшую спортивную семью.
9. Цеховым работникам разрешается спорить с конструкторами
Шлифовщик Сергей Докторов на вагоностроительный перешёл в 2011 году с авторемонтного завода, где получил пятый разряд. В совершенстве овладел плоской и круглой шлифовкой. На ВСЗ, в основном, занят подготовкой штампов для изготовления деталей.
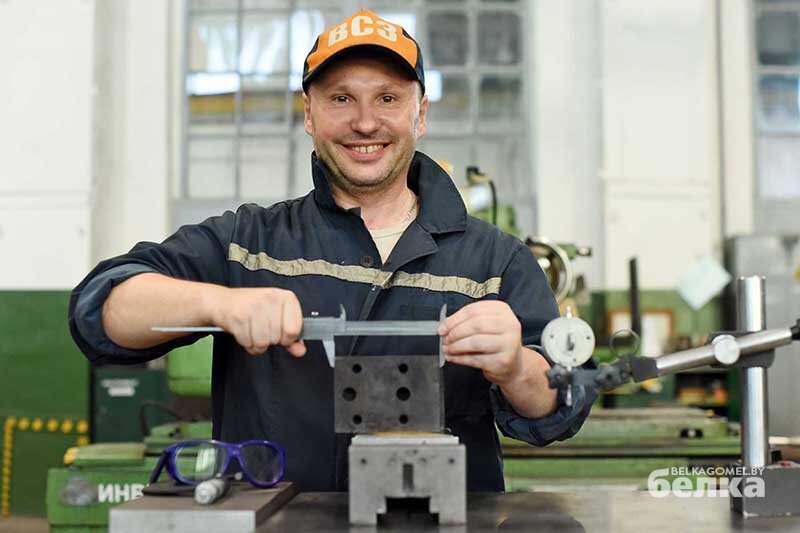
Сергей Докторов
Документация в инструментальный цех поступает из конструкторского отдела. Часто она вызывает у исполнителей вопросы, что приводит к полемике.
— Я знаю сферу применения своих изделий, знаю, какие требования уместны. А конструкторы закладывают размеры вплоть до микронов. Поэтому, бывает, спорим. Но только по делу, без эмоций. Если мы предлагаем что-то изменить прямо по ходу дела, автор чертежа приходит в цех, чтобы совместно найти приемлемое решение, — объясняет специалист.
Уникальность профессии Сергея Докторова заключается в том, что в училищах на неё не учат. Знания и навыки шлифовщики получают уже на предприятии, куда приходят работать, в соответствии с будущими задачами, которые предстоит решать. А вот разряды профмастерства есть, что видно на примере нашего собеседника. По специальности он, к слову, станочник широкого профиля, так что при необходимости может быть и токарем, и фрезеровщиком.
Когда Сергей Докторов устаёт от обработки металла, он отводит душу на спортивных площадках. Участвует во всех заводских соревнованиях по футболу, волейболу и настольному теннису, играет в городки, шахматы и шашки. Это помогает восстановить физические силы и получить эмоциональную разрядку.
10. На полную отделку одного вагона уходит три-четыре недели
Дмитрий Васильев работает в вагоносборочном цехе с декабря 1990 года. Интересно, что учился он на кулинара, а устроился на производство столяром. Учиться пришлось прямо на предприятии, за что Дмитрий до сих пор благодарен своему наставнику Нематджану Киргизову. Профессию освоил быстро, и с тех пор уже не рассуждал на тему «моё это или не моё» — всю жизнь работает на одном участке. А учёба продолжается.
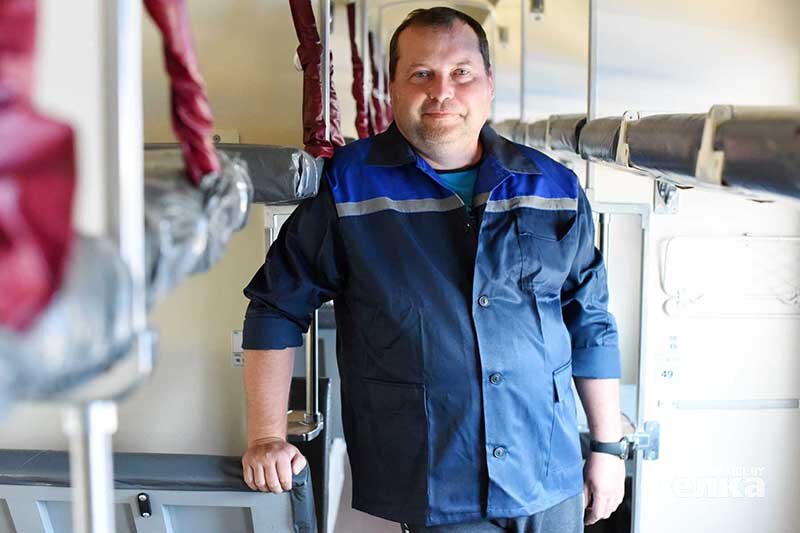
Дмитрий Васильев
— Сегодня применяются совершенно другие материалы и технологии. Постоянные пассажиры это наверняка и чувствуют, и видят. Наш участок занимается созданием в вагоне внутреннего каркаса, к которому крепится интерьер, настилом пола, утеплением и обшивкой стен, устройством перегородок. Всё, кроме окон и полок, — это моё, — объясняет Дмитрий Николаевич.
По словам Васильева, на полную отделку одного вагона в зависимости от его типа уходит три-четыре недели. Со специальными вагонами приходится повозиться дольше. У каждого из них своя планировка и особенности.
— За двадцать лет работы поменялись не только материалы, но и инструмент. Когда пришёл на завод, шуруповёрты были в дефиците. Сегодня у нас есть всё, и высокого качества,— говорит Дмитрий Васильев.
Автор: Светлана Коломиец, Евгений Захаров. Фото: Мария Амелина
Читайте также:
Чертёж маслёнки и сахарная голова Калинина: в музее Гомельского ВСЗ хранятся уникальные артефакты
В Гомеле дети заводчан нарисовали лето и попали в корпоративный календарь
Подпишитесь на наш канал в Яндекс.ДзенБольше интересных новостей - в нашем Telegram