В условиях санкционных ограничений гомельский литейный завод «Центролит» находит новые рынки сбыта, усиливая своё присутствие в России, и вкладывает собственные средства в модернизацию производства. О наработках последнего года и новых амбициозных целях в преддверии профессионального праздника металлургов беседуем с директором завода Сергеем Душко.
– Сергей Олегович, давайте напомним нашим читателям, на выпуске какой продукции специализируется «Центролит».
– Завод выполняет полный цикл работ, связанных с производством сложных литых изделий для станко- и машиностроения, нефтегазовой и металлургической промышленности, строительства шахт и метро. А это около 4000 наименований продукции. Возможности производства позволяют выпускать изделия от 500 граммов до 18 тонн из серого и до 12 тонн из высокопрочного чугуна. В настоящее время 45% продукции поставляется в Россию, 55% – в Беларусь.
Если же говорить о ежемесячных объёмах, то это в среднем 900 тонн чугунного литья. Технические и производственные возможности позволяют нам этот показатель увеличить до 1300 тонн.
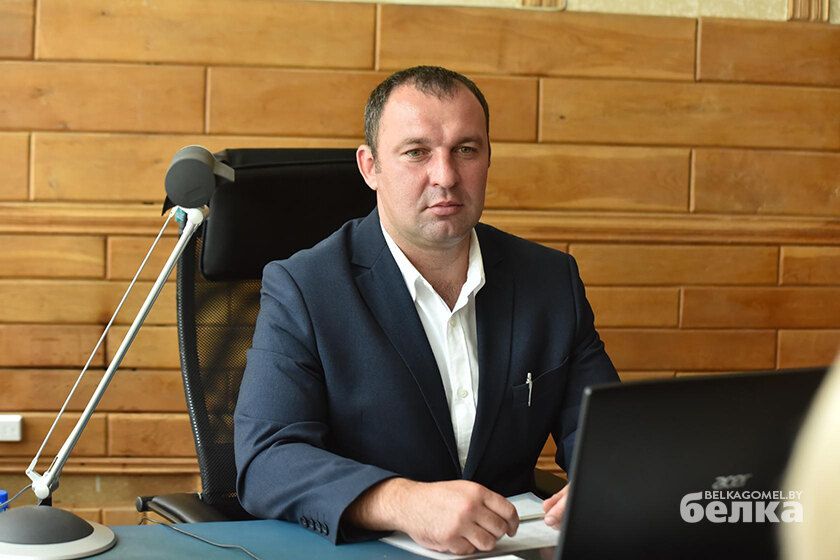
Сергей Душко, директор Гомельского литейного завода «Центролит».
– С мая в цехе №1 работает новый участок среднего литья. Знаю, что эту идею ваш коллектив вынашивал несколько лет. Если не секрет, сколько вложили средств и довольны ли результатом?
– Ещё бы. Теперь в нашем активе есть оборудование, позволяющее изготавливать отливки различной конфигурации, степени сложности и, самое главное, высокой размерной точности. В новый участок, в составе которого два смесителя, регенерация и выбивная решётка, мы вложили больше 1 млн белорусских рублей. Закупили его у российской компании «Родонит».
Энергоёмкость новой линии значительно меньше старого аналога, что отразилось на себестоимости выпускаемых отливок. Весовой диапазон изделий – от 50 кг до тонны.
– Вы сказали, что для России выпускаете 45 процентов продукции. Но у них же хватает своих литейных производств с давними традициями. За счёт чего выдерживаете конкуренцию?
– Отвечу так: за счёт инженерной мысли. Главный и самый жирный наш плюс – сохранение службы инженеров-технологов. Многие коллеги из России этим похвастать не могут. Наши специалисты берутся разработать конструкторско-технологическую документацию будущего изделия по представленному образцу, а иногда и просто фотографии. Часто так и происходит – с заказами различной сложности обращаются представители машиностроительных и станкостроительных компаний. Доводим всё до ума сначала в кабинетах, а потом работаем над отливкой в цехах, причём часто с дополнительными операциями – термообработкой и черновой механической обработкой под полным контролем технических служб.
– И сколько времени проходит от разработки документации до отгрузки изделия заказчику?
– Полный цикл производства может занимать до шести месяцев. На самом деле это не много, особенно когда речь идет об изготовлении станин. Стремимся и дальше развивать это направление. Берёмся за освоение тяжёлых отливок любой сложности и с повышенными требованиями.
– Можно говорить об уникальности продукции гомельского «Центролита»?
– Конечно. На участке точного литья выпускаются отливки корпусов турбин и корпусов подшипников для изготовления дизельных двигателей. Есть ещё у нас участок по выпуску непрерывнолитых заготовок: две линии непрерывного розлива чугуна позволяют своевременно выполнять заказы по производству заготовок из серого и высокопрочного чугуна диаметром от 40 до 200 миллиметров разного сечения – круг, квадрат, фигурный профиль. Только единичные предприятия на постсоветском пространстве имеют возможность производства по данной технологии. Основные заказчики такого литья – предприятия по производству гидроаппаратуры.
– Кто сегодня ваши крупные заказчики?
– Это в основном предприятия станко- и машиностроения – российская группа компаний «СТАН», в состав которой входят Ивановский и Рязанский станкостроительные заводы, калужский «Станкотех», московские «Шлифовальные станки», пензенский «ПТЦ «Привод». Из новых партнёров – «Ижнефтемаш», «ЗАРЕМ» (Майкопский редукторный завод), «Агат», Балтийский станкостроительный завод.
Вот буквально на днях у нас были представители станкозавода «ТБС» из Санкт-Петербурга. С этим городом с давних времён у нас тесные отношения, и связаны они в основном с поставками художественного литья. Как шутят наши литейщики, куда в Питере не пойдёшь, обязательно на наш фонарный столб или скамейку наткнёшься. Так и есть: большинство чугунных элементов уличной инфраструктуры на Невском проспекте гомельского производства. Но у «ТБС» интерес другой – предприятие специализируется на изготовлении средних и тяжёлых станков, так что их интересует наше крупнотоннажное литьё.
Отдельный большой сегмент — до трети всего производства — изготовление арматуры для дорожных и строительных организаций. Это всем известные дорожные люки, смотровые колодцы для инженерных коммуникаций, ливнеприёмники.
– А насколько сложно завоевывать российский рынок?
– Сложно, но на это сегодня нацелены все мои заместители и специалисты службы маркетинга. Эффективность работы каждого оценивается по проведённым переговорам и заключённым договорам. Постоянно мониторим площадки государственных закупок на территории России и заявились на получении сертификата, дающего право в них участвовать.
Откровенно скажу, процесс получения этого сертификата очень трудоёмкий, он потребовал сбора огромного количества документации: конструкторской, технологической, учредительной, коммерческой, по системе менеджмента качества. Но игра, как говорится, стоит свеч. Сертификат снимет любые вопросы при подаче документов на тендеры по закупкам для государственных и муниципальных нужд, автоматически повысит привлекательность нашей продукции в глазах производителей России. И это будет не экспорт ради экспорта, а выпуск продукции, реально влияющей на чистую прибыль.
– С какими белорусскими предприятия налажено сотрудничество?
– Тесные связи поддерживаем со всеми белорусскими станкостроительными заводами. Это «СтанкоГомель», Гомельский завод станочных узлов, столичный «МЗОР», витебский «ВИСТАН», оршанский «Красный борец». С этими предприятиями сложились очень тесные и взаимовыгодные отношения. Думаю, друг для друга мы останемся надёжными и долгосрочными партнёрами.
Пользуются отливками гомельского производства также машиностроительные предприятия. В их числе столичный «Амкодор», а также «БобруйскАгромаш», Бобруйский завод тракторных деталей и агрегатов, «Лидагропроммаш».
– Сергей Олегович, вы третий год руководите заводом. Какие планы созревают в вашей голове сейчас?
– Планы диктует жизнь, вернее, необходимость постоянно считать деньги. К примеру, как сэкономить на переработке металлургического шлака, а это более 1 млн рублей в год. Поэтому сейчас готовимся к воплощению в жизнь нового проекта – в 2022-2023 годах запустим свой участок переработки. Планируемое вложение – 420 тыс. белорусских рублей. А теперь сравните сумму с цифрой, которую назвал выше. Сначала отработаем тему для своих нужд, потом, а спрос, знаю, есть, заключим договоры с другими литейными предприятиями города.
Для понимания: в результате переработки металлургического шлака получается щебень вторичный, который используется в дорожном хозяйстве.
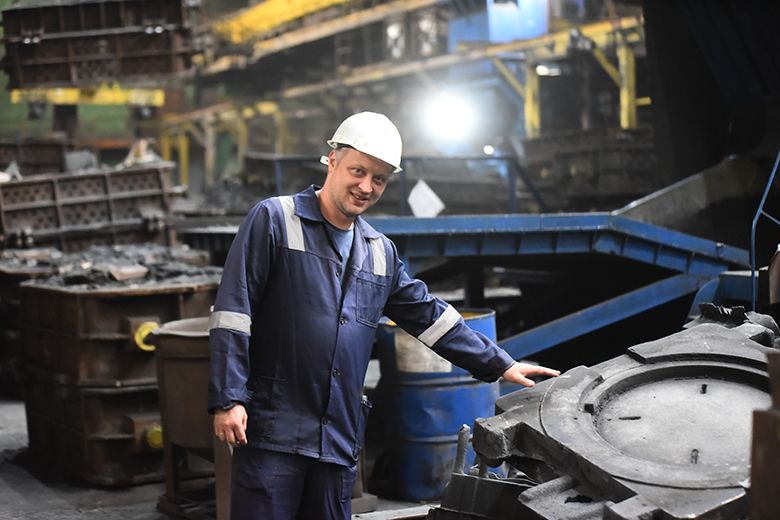
Евгений Зюзьков, главный металлург завода, из династии литейщиков.
– Расскажите о коллективе, много ли у вас молодёжи?
– Сегодня на «Центролите» работают 763 человека, из них 18% – ИТР, остальные – рабочие. Средний возраст работников – 40 лет, специалистов до 31 года – 17%.
У нас много трудовых династий: у кого-то отец работал на предприятии, у кого-то трудится брат, и так далее. Такие родственные связи сплачивают коллектив, повышают ответственность за конечный результат.
Молодых и перспективных тоже хватает. Но главное – им есть на кого равняться. Взять, к примеру, главного металлурга завода Евгения Зюзькова. Он из династии литейщиков, получил образование в техническом университете имени П.Сухого на факультете «Машинные технологии литейного производства». Окончил его с красным дипломом. Начинал на заводе инженером-технологом, сегодня он – высококвалифицированный специалист. О таких говорят – живёт работой. Человек, несмотря на опыт, постоянно занимается самообразованием, трудится в тесной связке с инженерами-конструкторами. А это звено предприятия заслуживает отдельной статьи в газете. Слова благодарности адресую Роману Белявскому, Валентине Цыганковой, Людмиле Ермоленко, Татьяне Лукашовой, Наталье Терещенко, Ирине Кацубо, Наталье Кушнеровой, Юлии Костюченко.
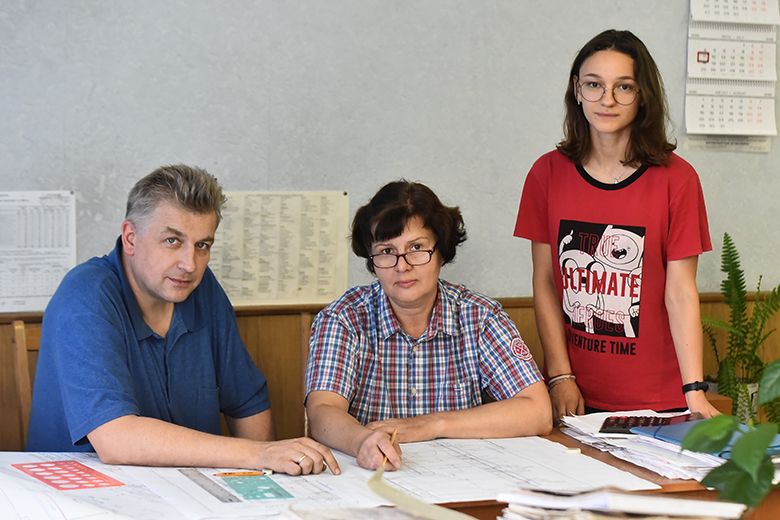
Роман Белявский, заместитель главного металлурга по технологической части, Наталья Магонова, инженер-технолог бюро крупного литья, Александра Жуковец, техник-технолог — молодой специалист.
Весь коллектив поздравляю с профессиональным праздником. Спасибо ветеранам завода, которые посвятили любимому делу свою трудовую жизнь и заложили традиции. Новому поколению заводчан желаю приумножать достижения своих наставников. Примите пожелания крепкого здоровья, счастья, душевной энергии и сил для новых свершений!
ЭТО ИНТЕРЕСНО
Фотокоры любят снимать заливку металла в формы. Да, со стороны выглядит красиво. Но только посвящённые знают, какой титанический труд стоит за этой красотой. На гомельском «Центролите» ходят легенды о силе местных рабочих.
***
Однажды пришёл на завод дзюдоист, гренадёрского роста, 120 кг веса. Увидел, как обычные с виду ребята на вытянутых руках носят ещё горячие после отливки тяжеловесные изделия. Решил попробовать. На третьей детали сдался.
***
А вот ещё случай. Мастер подходит к рабочему и спрашивает: «Почему деталь бракованная?». А он в ответ: «Где?!». И спокойно переворачивает крышку люка, словно и нет в ней 50 кг.
Верить подобным историям или нет — дело читателя, но то, что работа на литейном заводе требует выносливости и хорошего здоровья — факт.
Автор: Светлана Коломиец. Фото: Вячеслав Коломиец
Сейчас читают:
Лица гомельского химзавода: рассказываем о предприятии через истории людей
Подпишитесь на наш канал в Яндекс.ДзенБольше интересных новостей - в нашем Telegram